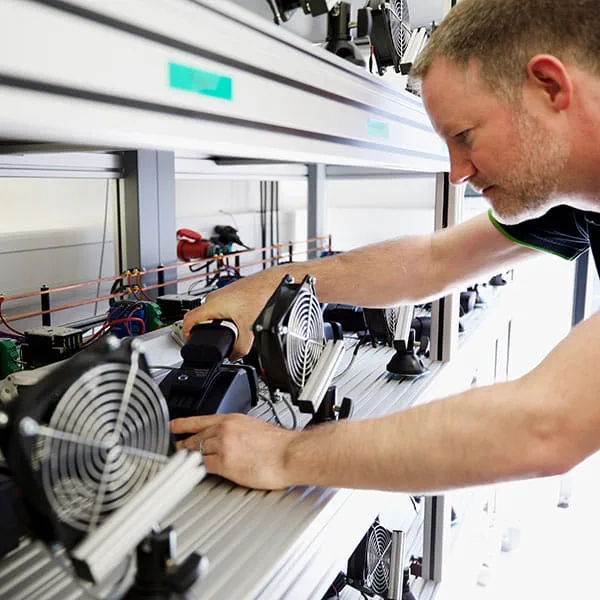
Passion with punishing standards
The Festool testing department is proving the machines to the breaking point
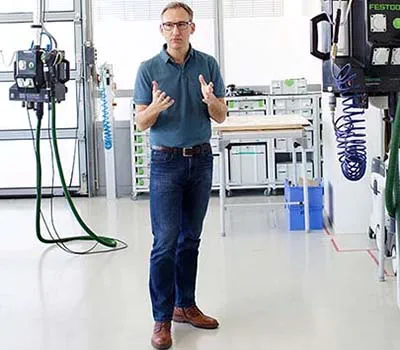
In the automotive industry, vehicles have to travel many millions of virtual and real kilometres before they are brought to market. Is it the same for Festool machines, too?
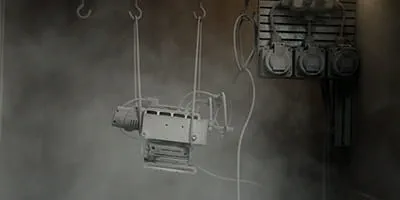
What conditions are the Festool devices subjected to in testing?
In the dust chamber, for example, sanders are operated in almost inhuman conditions and covered with dust. In the drop test, a cordless screwdriver is dropped onto a metal floor from a height of more than two metres, until it breaks – or not. We also use a compound mitre saw to saw a concrete block, which nobody would seriously do.
All this is done for the benefit of the customers?
That’s right. Our machines are all known for being capable of doing a slightly better job and lasting significantly longer than comparable devices on the market. That is our top priority. And that is precisely what we ensure with our extensive series of tests and trials. Besides robustness and durability, the health of users is also a major concern for us.
So the machines have to withstand more in these extreme stress tests than they would when used by customers later?
The quality goals we want to achieve are very high. Of course, there are the guidelines and standards of the International Electrotechnical Commission (IEC). The requirements laid down there are an important foundation, but in many cases we even go beyond these. It is important for us that we not only measure the performance values but that we also test how a machine feels. For us, it’s always about touching, too. In the acoustic chamber, for example, it’s not just about reducing the volume but also reducing individual frequencies which, whilst they may not be loud, are extremely unpleasant. We filter out and minimise these frequencies.

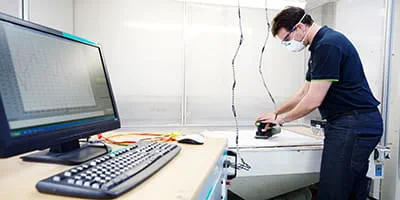
You have had joint responsibility for quality management at Festool for some time now. You have also been head of testing for two years. What is the difference?
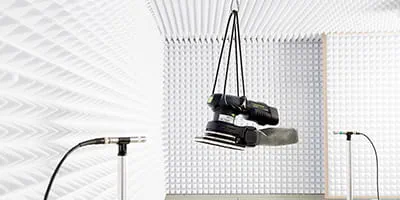
So that means there are a lot of threads diverging from and converging on the testing department then?
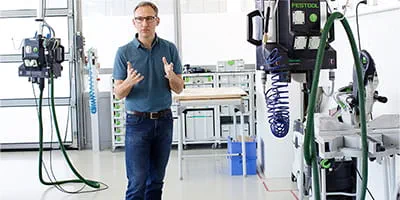
For testing, does this mean faster but in no way less careful?
What appeals to you about your work in particular?
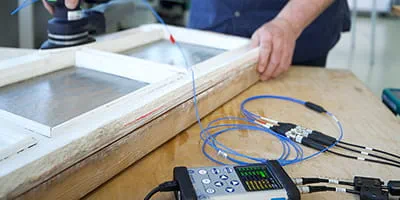