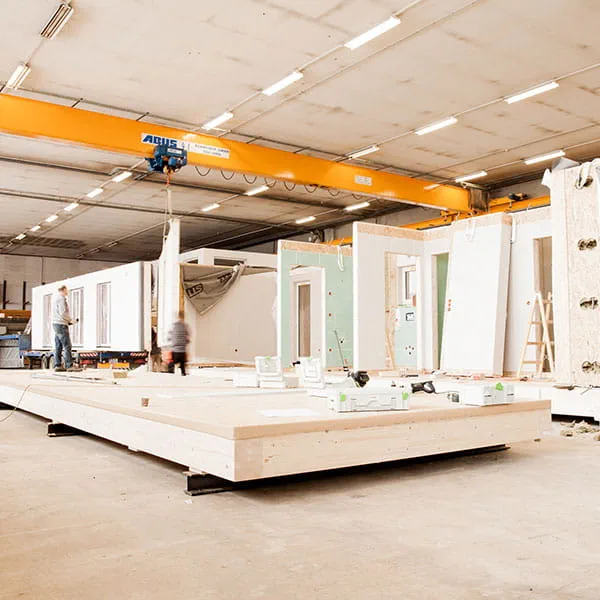
Clever construction – flexible living
Innovative construction meets efficiency. A visit to Haas Fertigbau in Austria.
Quicker and less expensive to build while still offering a cosy atmosphere: Modular houses are the latest trend in pre-fabricated building construction. Manufacturers of pre-fabricated houses are faced with brand new practical challenges. Innovative solutions are in demand, efficient working an absolute must. We discovered what that means during a visit to Haas Fertigbau in Austria.
Graz is the regional capital of Austria's south-eastern state of Styria, and the area surrounding the city is generally known for its atmosphere of ease and idyllic landscapes. Locals also call it the "Grüne Mark" (green march) for this very reason. But on this morning in January, there's nothing to be seen of forests, meadows and Styrian equanimity – it's been snowing since the early hours. There's chaos on the roads. But operations at Haas Fertigbau in Großwilfersdorf don't seem to be the least bit affected. A forklift truck is currently loading several wall elements onto a lorry. A finished modular home greets visitors entering the company premises. This is where we meet Markus Schweinzer. He is the technician responsible for the relatively new modular building concept at Haas.
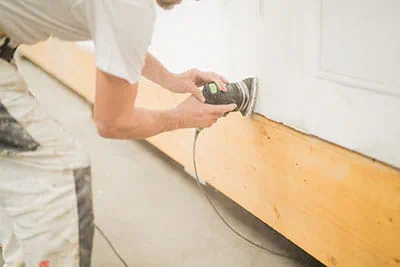
Clever construction, flexible living
"The idea for the clever FlexHome modular construction concept came about in cooperation with Graz University of Technology," explains Schweinzer while we walk towards the production line. "Our customers prefer flexible living solutions, because they don't want to be shackled to one location. The modular FlexHome can be used as a living space, office, weekend home, mobile home or doctor's surgery, to name just a few options. That means a great deal of flexibility for our customers."
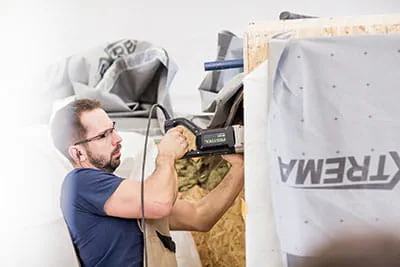
Screwdriving with torques of 98 newton metres
In the assembly building, a familiar power tool is waiting for us: An employee is drilling holes for screw connections in the wall elements with the Festool QUADRILL DR 20. Depending on their size, the individual elements weigh between 200 and 1500 kilograms. The employee has no reason to expect any resistance from the wooden panels: The corded powerhouse is unstoppable when drilling precise holes in wood with a torque of up to 98 newton metres. And delays are certainly not wanted for this task; after all, the next wall element is already waiting for assembly. For screw connections around corners, the DR 20 is used in combination with the elbow attachment. Four pre-fabricated walls are assembled for each house. "We mainly use wood from the region for our modular FlexHomes," explains Schweinzer.
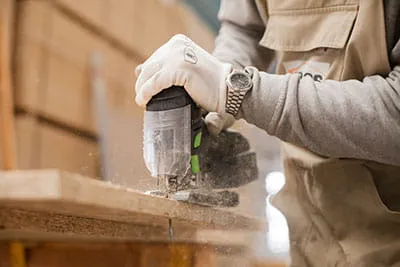
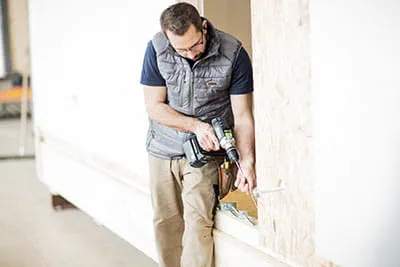
"What matters for us is precision and speed. The timing of the work processes has been coordinated perfectly."
Fertigbau Haas employee
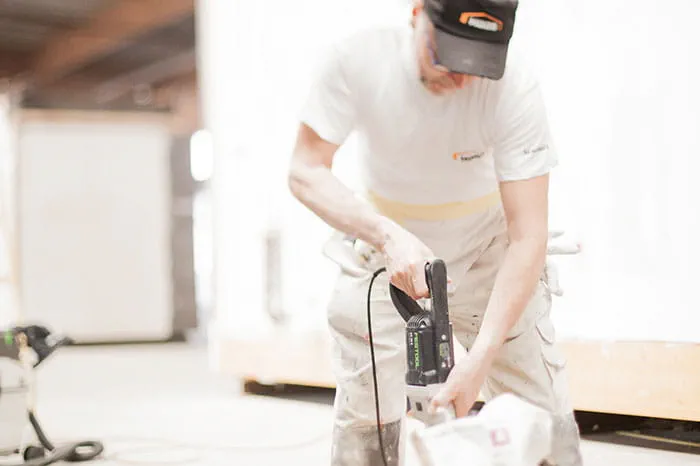
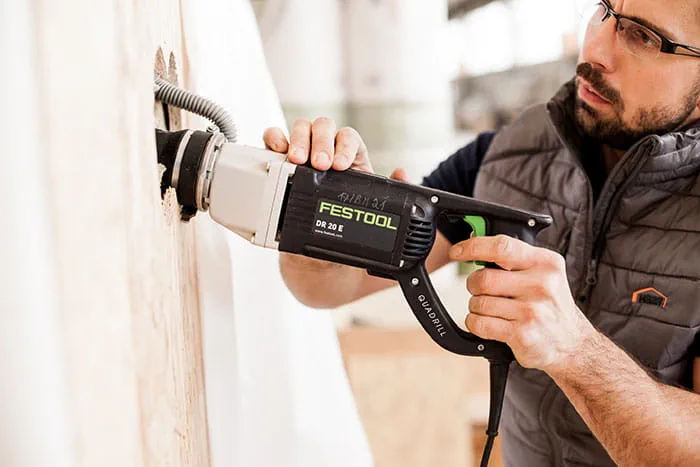
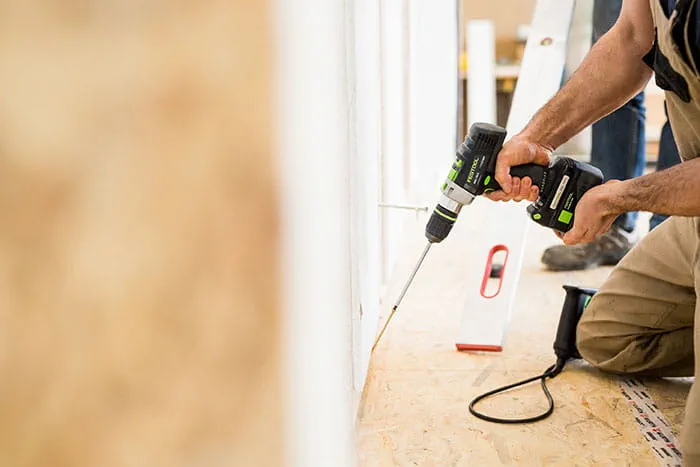
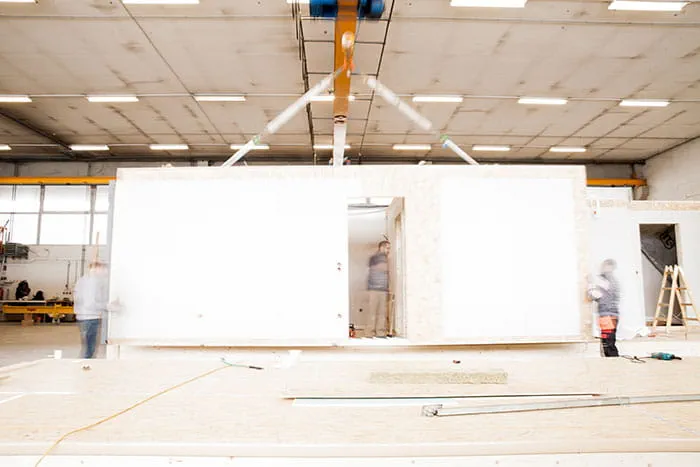
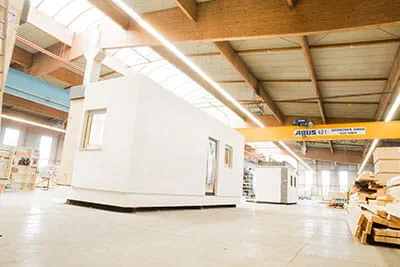
A triumph of precision and speed
It's a bit like a Formula 1 pit stop when the 20 to 25 members of the assembly team work on the different modules. But things never get hectic, since the team along the production line is very experienced. "What matters for us is precision and speed. The timing of the work processes has been coordinated perfectly, so that there are no idle times," one of the workers tells us. "Mobility in the production environment plays an important role for us so that we can move freely along the production line during the assembly process. Cables often end up being trip hazards and restrict our movements. That is why we mainly rely on cordless tools like the PSC 420 jigsaw or the PDC impact screwdriver."
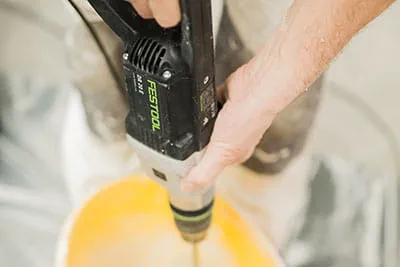
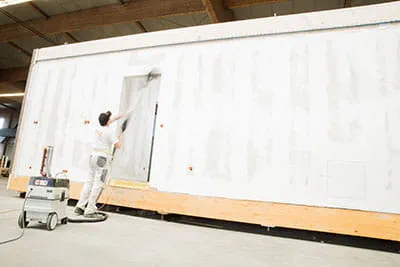
The final touches
As soon as the basic structure has been assembled, it's time for the interior finishing of the modules. The undercoat is quickly stirred with the QUADRILL DR 20 and the clip-on stirring attachment. In the next step, the surface is sanded with the PLANEX LHS 225 long-reach sander until it's perfectly smooth and then plastered. "What really matters is using the right abrasive with the right grit. A fine grit is ideal for achieving a good surface finish for softer materials. If you use an abrasive that is too coarse, you might end up actually scratching the surface. That would result in costly rework. So we always take care to prepare surfaces as perfectly as possible," explains the employee responsible for this step.
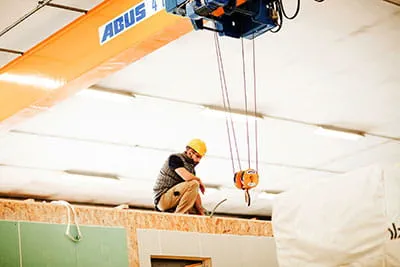
A house on the hook
At the end of the production line, a module is currently being loaded onto a lorry. A major feat, not just for the crane: The manoeuvre demands great physical effort and cool heads from the entire team. Each motion has to be just right, because even minor damage to an exterior wall can have major implications once the house is exposed to the elements. Transport also requires a great deal of care, since the lorry is transporting an oversized load with a house 3.50 metres wide and weighing 16 tonnes. "It currently takes us four weeks to manufacture a complete modular house in our plant. But we are optimising our processes to make the procedure even quicker. There's a great deal of demand," Markus Schweinzer tells us as we are leaving the production buildings. We are certain: FlexHome is an innovative living concept that is fit for the future.